Laudert establishes stringent workflows for dynamic publishing
Over 12,000 print items for 1,000 articles: Remmers is internationally known for its paints and varnishes. Together with Laudert, the company has automated its label printing on the basis of the priint:suite in order to adapt to the constantly changing labeling requirements and formulation changes. A prime example of the effectiveness of dynamic publishing.
Founded in 1949, Remmers, a family-owned company with 15 independent subsidiaries and sales agencies in over 30 countries, specializes in the manufacture of construction chemical products, wood paints and varnishes, and industrial coatings. Around 1,500 highly qualified specialists are employed for this purpose.
High manual effort
Replacement of manual work steps
In order to be able to respond to changes in formulation or legal requirements at short notice when printing labels for the company’s own products, label printing was transferred to a highly automated workflow. Key objectives: Time savings compared to the previous process and a high level of production reliability while minimizing errors.
Remmers keeps the necessary information for the labels in a PIM system. From there, they were previously transferred manually to the corresponding documents via drag & drop and placed by hand. An unbelievable amount of work: Ingredients subject to certification, hazard warnings, color tones, backgrounds, icons, automatically generated QR codes, information on export subsidiaries and much more had to be placed on the labels – and in eleven languages.
PIM and priint:suite working together
GameChanger Workflow Automation
For Laudert, it was therefore clear that in order to replace manual work, which is not only time-consuming, but also error-prone, automation was essential. To this end, workflows were set up that are divided into clear steps and can be transparently tracked at any time. The starting point is the PIM system, which keeps the necessary data up to date and automatically initiates workflows for the creation of new labels. Laudert implemented WERK II’s priint:suite as the central software for layouting. It directly accesses data from the PIM, so that layouting can be carried out with up-to-date data:
Instead of small-scale, manual fine-tuning, the workflow follows layout specifications for a complex, automated structure of the labels according to aspects of legal requirements and corporate design. The PDFs generated from InDesign are fed back to the PIM and then trigger the correction process. All workflows run stringently and are secured via release stages. This minimizes errors and guarantees the correct structure of the labels. Variant creation is also triggered automatically.
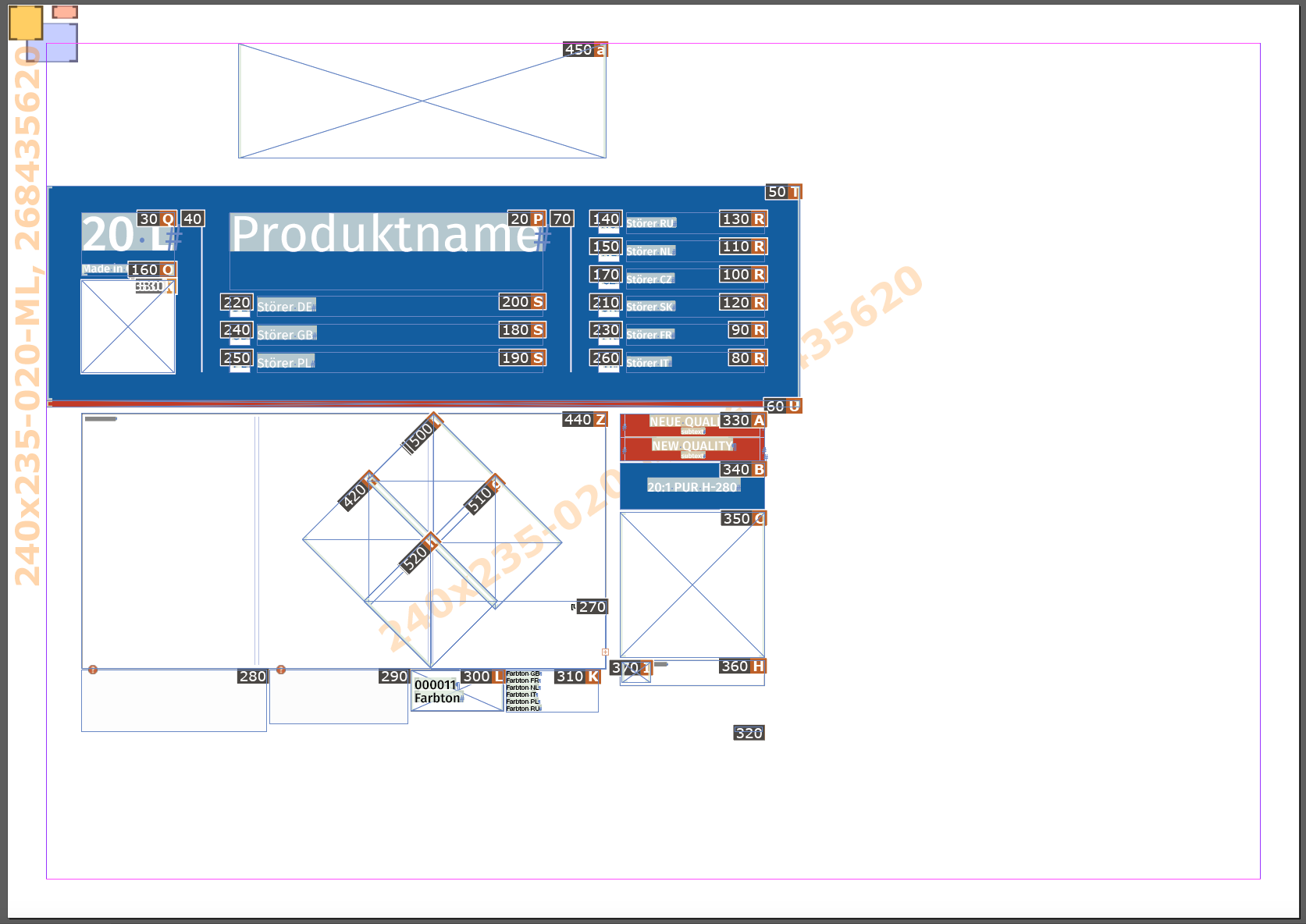
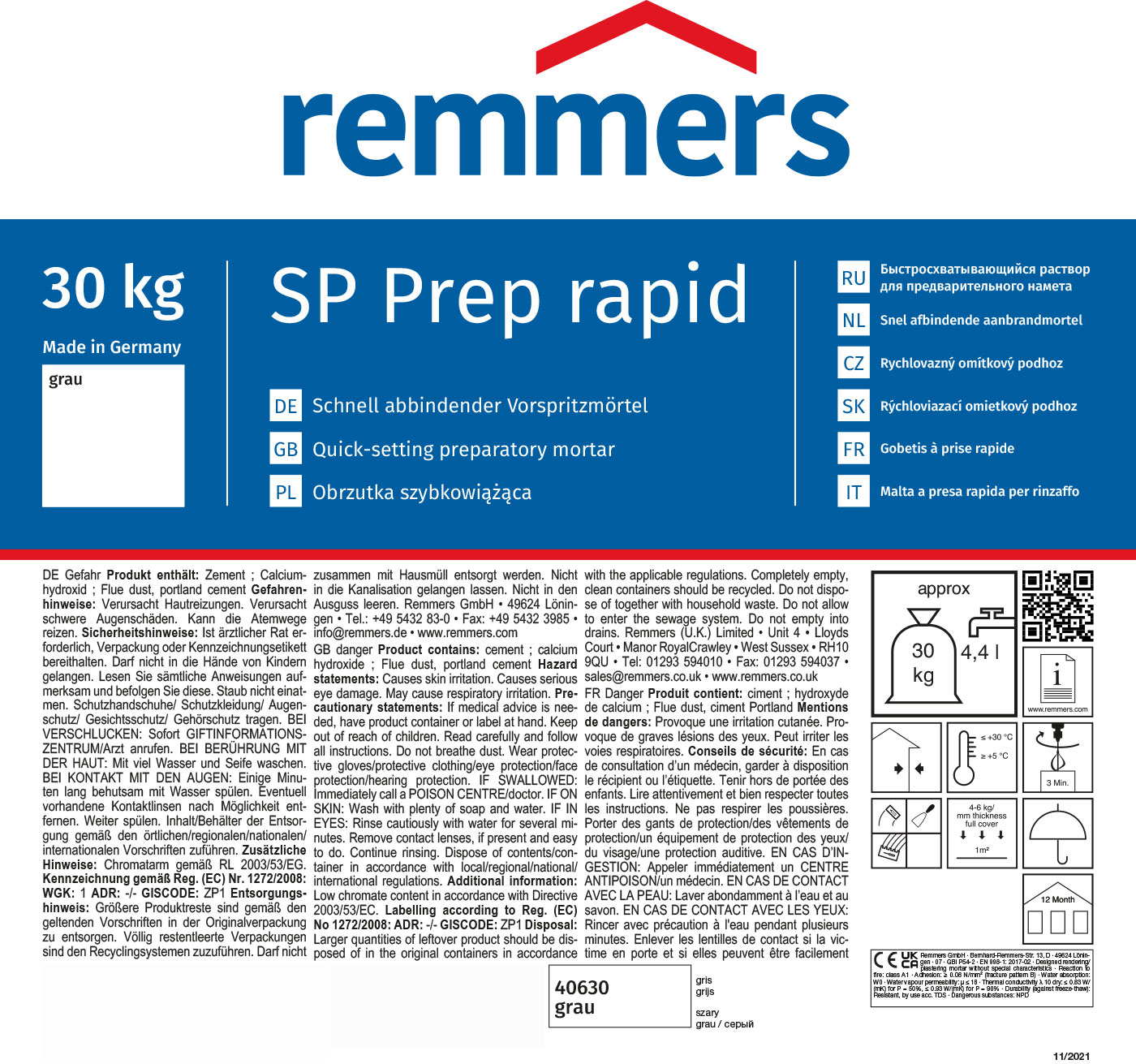
Based on the placeholder layout, the label is built automatically.
Fully automated despite complexity
Intelligent label logic
Anyone familiar with labels on paint buckets knows how complex they are. The logics that contribute to the creation of documents in the priint:suite are correspondingly sophisticated.
The fully automated template control takes into account, among other things the exact positioning, font sizes in relation to container sizes, page changes, text circulation and image placement. The different text flow in the various languages also plays a decisive role and is automatically taken into account.
The only exceptions to full automation are very small margins and special products. In these rare exceptions, partial automation is used to provide the best possible support for the the label production process in the best possible way.
Copy & Paste is history
What automation means for remmers
André Bias, Prepress/Print Shop Manager at Remmers, emphasizes, “Thanks to automation, our label production is really fun. The time when the sword of Damocles hung over Remmers prepress is over – as is the time of copy & paste, which led to faulty label production.”
Thanks to the stringent workflows, the high level of automation, the ability to react quickly and easily to market changes, and the high level of production reliability combined with an enormously low susceptibility to errors, acceptance by employees is also a given. And because it works so well, the printing of brochures is now also being carried out on the basis of similar workflows implemented by Laudert.